Abrasive Blast Cleaning
Our abrasive blasting process removes all contaminants, including rust, paint, and grease, from your assets, ensuring a clean and smooth surface for coating. Our experienced operators can create a variety of surface profiles and cleanliness level depending on the type of coating specified in the project, which helps to improve adhesion and extend the lifespan of the coating. At SVE, our abrasive blasting services are at par excellence with the industry standard. With expertise in both in-house and on-site applications, we employ various media such as garnet, steel grit and slag abrasives. Our refined blasting processes consider surface type, environmental factors, and equipment involved for achieving following industry prevailing surface preparation standards.
- Brush off abrasive blasting NACE-4 / SP-7 / ISO:1
- Industrial abrasive blasting NACE-8 / SP-14
- Commercial abrasive blasting NACE-3 / SP-6 / ISO:2
- Near white abrasive blasting NACE-2 / SP-10 / ISO: 2 1/2
- White metal abrasive blasting NACE-1 / SP-5 / ISO: 3
Horizontal vacuum Blast Cleaning-Dust free blasting
SVE dust free vacuum steel blast cleaning process has a great production width and offers a higher productivity rate for larger jobs without disturbing nearby concurrent work activities. This is the perfect process for large horizontal steel surfaces such as ship decks, steel plates, oil platform helicopter decks and walkways and bridge decks.
Spray painting (Protective Coating)
After satisfactory surface preparation we are able to provide complete coating application services and have the specialized equipment and expertise to apply all type of materials and finishes. Application of paint by airless spray machine to steel structures, crude oil tanks, heavy equipment, pressure vessels, machinery, galvanized item etc
Brush / Roller painting (Protective Coating)
The hand application of industrial coatings to the highest standards. Application of paint by brush / roller to steel structures, piping, supports, pressure vessels, machinery, galvanized item etc. We offer a variety of paint and coating systems to choose from, tailored to your specific needs and budget. Our team of experienced and certified painters ensures a long-lasting and durable finish. We have a rigorous quality control process in place to ensure that all coatings meet our high standards.
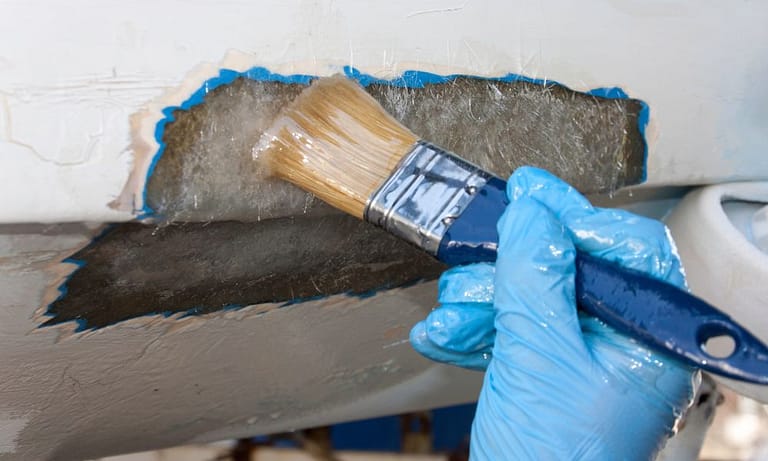
Thermal Spray application (Protective Coating)
Thermal spraying uses heat, depending upon the metallurgical properties of the coating material, depending upon the thermal spray process. Each process has different benefits as the result of these temperatures and process characteristics. A thermal spray process is carefully selected depending upon the desired coating characteristics such as; wear resistance, corrosion resistance, thermal barrier, and many more. Other factors include: size and shape, substrate material and the operating environment of the component. Our operators are well experienced in using thin & thick wire arc metalizing machines including THERMION USA make units.
High build epoxy / polyurethane (Protective Coating)
A two-component high solid epoxy / polyurethane coating application provides excellent protection in demanding environments and is especially suited as a tank coating in petroleum products industry.
Glass flake epoxy coating (Protective Coating)
A two-component high build glass flake application for steel structures on offshore splash and submerged zone structures, Industrial plants, bridges, tank exteriors, oil tanks, pipelines, marine atmosphere, cooling towers, etc. It provides good resistance to spillage and fumes of acids, alkalis, fresh and salt water. The performance of this product depends upon the degree of surface preparation and experience of applicator.
Epoxy / Polyurethane floor coating & water proofing solutions
Our Epoxy flooring services are extremely highlighted for its marvelous strength, life-long efficiency, appealing look, and easy maintenance. The coating is done perfectly according to customer’s choice so as to provide complete satisfaction. Moreover, our skilled personnel firmly follow all quality parameters & standards in providing these services to certify fivestar level. We make utilization of trend setting innovation and gear to render the ground surface administrations in the most ideal way. We offer floor coating services and waterproofing solutions for the large construction industry and protective coating solutions for metal and concrete enterprises.
Intumescent Coating
A coating for steel that can give a highly decorative finish. It works by expanding in a fire, creating a dense char and keeps the failure temperature of the steel below its critical failure level for periods of up to 3 hours Safe, durable and affordable, Intumescent fireproofing is a thin film coating that is applied directly to a variety of otherwise unapproved building materials, allowing them to meet fire code, fire rating and flame spread requirements. Intumescent fireproofing coatings are used indoors and outdoors, can be environmentally friendly and have been proven in service over many years. Intumescent high performance paint can keep construction costs low while preserving focal points and building character. Our crews utilize specialized surface preparation and application techniques when applying fire retardant coatings to doors, columns, and structural steel or as a coating for fire stops, ducting voids and other smoke and fire prevention applications.
Cementitious Coating
Cementitious fire spray is a fast and efficient method of providing up to 3 hours fire protection to structural steelwork. Used in the commercial, petro-chemical and tunnels markets, cementitious fire sprays withstand impact and abrasion, yet remain flexible to accept design changes without incurring major cost and time delays.
High pressure water jetting (SP 1 / ISO 8504)
Loosely-adhering material: 100%
Tightly-adhering material: 100%
Stains, streaks, shadows: 100%
Abrasive blasting won’t remove oil and grease – it just smears them over the surface, causing premature coatings failure. Visible deposits of oil, grease and dirt must be spot cleaned prior to abrasive blast cleaning. SP 1 is a prerequisite to the other SSPC abrasive blasting specifications.
The standards specify numerous methods for solvent cleaning. The most common method – and the least effective – is washing with soap, water and a rag. A dirty rag will also smear grease and oil: care must be taken to wipe, fold, repeat, and replace often. For large surfaces, pressure washing with soapy water is recommended, although soap residue will inhibit coating adhesion and should be rinsed off.
Steam Cleaning
For degreasing Operations utilizing a range of pressure and temperatures for high quality surface preparation. To provide the level of preparation tailor made to suit the coatings specification.
Paint Stripping
For specialist operations in sensitive areas (eg. turbines, motors, etc.) using paint removal chemicals. For use on surfaces where blasting would be impossible. The chemicals are washed off after use leaving surfaces free for further application.
Power Tool Cleaning
Surface preparation using a range of hand-held tools (eg. needle guns, grinders, sanders). For use in areas where the high cost of abrasive blasting is not justified).
Inspection Testing & Monitoring
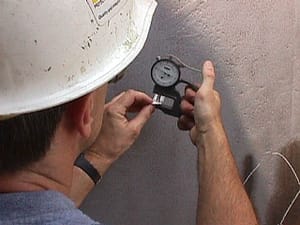
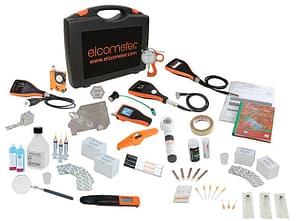
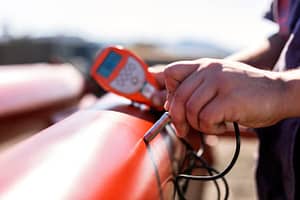
We have in our possession the most modern “State of the Art” equipment for testing of surfaces being coated and to monitor atmospheric conditions while application of paint so as to comply with the standards promulgated by various international paint manufacturers. We aim to provide integrated, empowering, and cost-effective crew hiring solutions for various categories available for short-term and long-term jobs. We currently deal in offering qualified brush/roller painters, abrasive blasters, grit blasters, hydro blasters, airless spray painters, supervisor and riggers among others. Whether you need one person or an entire project team, we match the right candidates to right opportunities and provide seamless support throughout the employee lifecycle.
cutting-edge coatings provide resistance to corrosion and abrasion, while protecting surfaces from galling, seizing and other metal surface damage. Our teams strive to enhance personnel and equipment safety while offering superior, expedited service to fit the needs of the petrochemical industry.
Oil Tank Coating
Years of service and chemical corrosion can harm the inside of tank preventing it from properly protecting its contents. Tank lining and coating is a key factor in preventing not only product contamination but also corrosion. A wrong choice of tank surface preparation may result in lack of adhesion, solvent entrapment from applying multiple coats too quickly, soluble salt contamination, and/or inadequate ventilation and post cure requirements. We ensure you to get the best possible surface preparation and provide a broad spectrum of surface coating solution of industrial tanks. Our services include standard surface preparation, internal and external coating application.
Pickling, passivation on Ferrous & Non-ferrous material
SVE has an experienced team of technicians for carrying out Pickling & passivation activities on ferrous and nonferrous material as a metal finishing process that removes impurities such as rust, scale, and oxide layers, from the surface of a metal. Followed by passivation process to protect the surface of metal from corrosion.
Color coding, stencilling, flow direction marking and labelling.
Labelling pipes in an industrial facility or field setting can seem daunting, but with the proper information, the task is simple and SVE team of operators are well experienced in executing flawless pipe marking which is crucial for compliance with industry standards.
Structural Coating application
Surface preparation is the essential first stage treatment of a steel substrate before the application of any coating, and is generally accepted as being the most important factor affecting the total success of a corrosion protection system.
The performance of a coating is significantly influenced by its ability to adhere properly to the substrate material. Residual mill scale on steel surfaces is an unsatisfactory base to apply modern, high performance protective coatings and is therefore removed by abrasive blast cleaning. Other surface contaminants on the rolled steel surface, such as oil and grease are also undesirable and must be removed before the blast cleaning process.
The surface preparation process not only cleans the steel, but also introduces a suitable profile to receive the protective coating. Paint specifications usually comprise a sequential coating application of paints or alternatively paints applied over metal coatings to form a ‘duplex’ coating system. The protective paint systems usually consist of primer, undercoat(s) and finish coats. Each coating ‘layer’ in any protective system has a specific function, and the different types are applied in a particular sequence of primer followed by intermediate / build coats in the shop, and finally the finish or top coat either in the shop or on site. We provide the ‘best value’ service to maximize coating performance over structure life and to reduce whole life costs.
Marine Coating applications
Our marine paints and coatings application are applied to fixed and floating marine structures such as offshore oil rigs, and recreational boats and yachts, petrochemical, Refinery and Chemical assets. Included are passenger ships, freighters, tankers, container ships, fishing boats and ferries, as well as oil rigs, inland waterway ships, barges and tow boats.
Our marine coatings services are designed with particular functionality properties to best protect and preserve the surfaces to which they are applied. Coatings are applied in accordance with paint manufacturer’s guidelines with all necessary criteria being met prior to commencement of coating and of course carefully complied with during the coating process.
Pipe Coating applications
Steel pipelines are used all over the world for cross country transport of natural gas, crude oil, water, petrochemical and petroleum products at high pressures over long distances. These pipelines are protected against corrosion by external and internal coating systems External coating primarily acts as a barrier between the pipe and its surrounding environment. It is one of the main methods used to protect pipelines from corrosion – often used in conjunction with cathodic protection – and can also provide thermal insulation. An internal coating can be applied to reduce friction within a pipeline and enable smoother product transmission, resulting in increased product throughput, reduced operational costs, faster commissioning, and corrosion protection in storage. Internally coating a pipeline also causes less wear to pigs during runs. Depending on customer specifications, we offer Liquid epoxy coating or Special anticorrosive painting.
Equipment Coating
Equipment are probably the most complicated area to protect. Besides the pressure itself, there are challenges in the chemical processes in the vessel and the temperatures that often accompany them, and it is important to be clear on the exact needs. Metal Coatings supplies refineries and gas companies with safe, durable and cost-effective coating services for petrochemical corrosion protection that we also perform on a variety of substrate types.
Providing skilled experienced craftsmen for project works
We provide highly qualified professionals and skilled labours to support with the best work force. We skilled craftsmen to reduce the worries of our customers. Thanks to our unflinching commitment to the best interests of the businesses and job seekers, we have gained the reputation of being a reliable, lair-minded and straight forward manpower supplier. We provide exclusive and qualified Coating process workforce for all sectors like Oil and Gas, Mechanical Construction, Electrical, Marine & Ship Manufacturing, Power and desalination plant.